بازیابی و استفاده مجدد از پساب
رشد پیوسته جمعیت،آلودگی آبهای سطحی و زیر زمینی،توزیع غیریکنواخت منابع آبی و خشکسالی های دوره ای،سازمان ها و متخصصین آب و فاضلاب را مجبور کرده که به دنبال منابع جدیدی جهت تأمین آب باشند. تکنولوژی استفاده از پساب تصفیه شده فاضلاب با کیفیت بالا به عنوان یک منبع آب قابل اعتماد، توجه زیادی را به خود جلب کرده است. امروزه با پیشرفت تکنولوژی و ابداع روش های تصفیه پیشرفته فاضلاب می توان بخش عمده ای از فاضلاب های تولید شده در صنایع و نیز فاضلاب های بهداشتی را مورد تصفیه قرار داده و پساب تصفیه شده را به سیکل استفاده مجدد بازگرداند.
تصفیه آب برای حذف باکتریها و انگلهای مضرر موجود در آب لازم و ضروری است. بعضی از این باکتریها باعث بروز بیماریهای میشود که ممکن است هفتهها به طول انجامد. این باکتریها و انگلها حتی میتوانند برای ماهها در محیط باقی بمانند. این پاتوژنها به طور مؤثر توسط عبور آب از طریق فیلترهای میکرو و نانو فیلترها موجود در دستگاه تصفیه آب حذف میشود. همچنین با توجه به قرار گیری کشور ما در منطقه کم آب جهان و محدودیت دسترسی به منابع آبی در بخش وسیع از کشور، استفاده از فاضلاب تصفیه شده در مصارف گوناگون می تواند گزینه بسیار مناسب و مقرون به صرفه جهت تامین آب مورد نیاز صنایع مختلف باشد که در عین حال منجر به حفظ منابع آبی موجود و جلوگیری ار اتلاف آب و آلودگی محیط زیست نیز می شود.
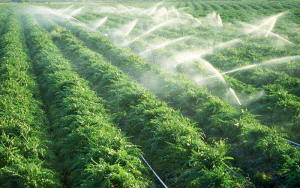
سیستم تصفیه فاضلاب بازیابی و استفاده مجدد از پساب
در همین راستا شرکت عمران سازان مهاب با تکیه بر دانش فنی متخصصین خود و با بکارگیری جدیدترین تکنولوژی ها اقدام به طراحی، ساخت و اجرای انواع سیستم های تصفیه پیشرفته فاضلاب با هدف بازیابی و استفاده مجدد از پساب و در عین حال کاهش هزینه های مربوط به تامین منابع آبی مورد نیاز صنایع می نماید. روش تصفیه فاضلاب و نوع سیستم انتخابی جهت بازگردانی و استفاده مجدد از پساب تابع نوع پساب تولید شده اولیه، کیفیت پساب اولیه، نوع کاربرد پساب بعد از تصفیه و کیفیت مورد نیاز پساب جهت بازگردانی و استفاده مجدد می باشد. لذا با توجه به گستردگی روش های تصفیه نوین و نیز کیفیت های بسیار متفاوت فاضلاب به ویژه در مورد فاضلاب های صنعتی، انتخاب روش تصفیه فاضلاب نیازمند بررسی و مطالعه جامع از وضعیت موجود و تعیین ویژگی های پساب اولیه می باشد.
موارد استفاده از پساب تصفیه شده
آبیاری کشاورزی
آبیاری مناظر طبیعی
فعالیت های صنعتی بخصوص در بخش فرایند و خنک سازی
شارژ منابع آب زیر زمینی
مصارف تفریحی و زیست محیطی
مصارف غیر شرب شهری
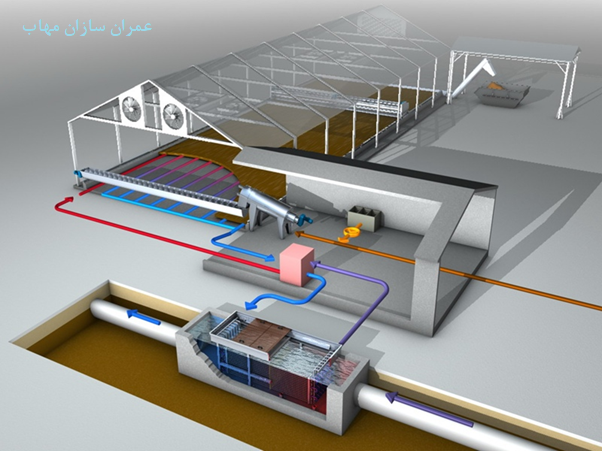
بازیابی استفاده مجدد از پساب Water Treatment Reuse
توجه به رشد روز افزون پساب های صنعتی فناوری های پیشرفته ای نیاز است تا ترکیبات خطرناک موجود در فاضلاب ها را حذف نماید. تکنولوژی های نوین تصفیه نظیرانواع سیستم های فیلتراسیون غشایی، فیلتراسیون با متغیر خودکار (AVF) ، روش اکسیداسیون پیشرفته (AOP) ، اشعه ماورا بنفش پیشنهاد و آزمایش شده اند. نتایج نشان داده که استفاده از این روش ها در حذف آلاینده های حاصل از فاضلاب موثر بوده است.
درصورتی که با نصب دستگاه تصفیه آب صنعتی مناسب، پیش از ورود آب به این سیستمها، میتوان در هزینههای تعمیر و نگهداری صرفهجویی کرد. اصلیترین دستگاه های تصفیه صنعتی آب عبارتند از:دستگاه اسمز معکوس، دستگاه سختیگیر، دستگاه اولترافیلتراسیون، دستگاه الکترودیالیز. در یک دسته بندی کاربردی دیگر دستگاه های تصفیه صنعتی به دو دسته کشاورزی و دریایی تقسیم بندی می شوند. دستگاه تصفیه آب صنعتی در صنایع حساس به آلودگی و شوری مانند داروسازی و سرم سازی، آشامیدنی، تصفیه آب کشاورزی، دارویی، لبنی، غذایی و معادن به کار برده می شود و هدف اصلی آن کاهش شوری، املاح، آلودگی و سایر عوامل آلاینده از آب می باشد. با توجه به نوع فرآیند و روش های تصفیه آب صنعتی، هر یک از دستگاه ها ویژگی ها و مزایای مشخصی دارند. این روش ها عبارتند از
- تصفیه صنعتی آب به روش سیستم تبادل یونی
- تصفیه صنعتی آب به روش سیستم اولترافیلتراسیون
- تصفیه صنعتی آب به روش سیستم میکروفیلتراسیون
- تصفیه صنعتی آب به روش سیستم نانو فیلتراسیون
- تصفیه آب به روش EDI
- تصفیه صنعتی آب به روش Electro dialysis Reverse
- تصفیه آب به روش سیستم اسمز معکوس ( RO )
- تصفیه آب صنعتی بر پایه روش حرارتی
بسته به نیاز صنایع از انواع دستگاه آب شیرین کن صنعتی استفاده می شود. در این سیستم ها هر گونه باکتری ها و آلاینده ها حذف می شود. به همین دلیل یکی از مهمترین مزیت های دستگاه RO کاهش هزینه های مصرف آب و انرژی می باشد. مهم ترین مزایا عبارتند از:
- اقتصادی بودن سیستم نسبت به روش های دیگر
- مصرف انرژی کمتر در مقایسه با روش های دیگر تصفیه آب
- امکان کار مداوم بدون نیاز به توقف های ادواری
- سهولت کار با دستگاه و کاهش هزینه های تعمیرات و نگهداری
- عدم عبور باکتری، ویروس ها و مواد تب زا از ممبران ها
- امکان بازگرداندن آب غلیظ به محیط زیست
طراحی فرآیندهای آب شیرین کن با توجه به پارامتر های مانند دبی آب مورد نیاز ، کیفیت آب ورودی و خروجی و …. صورت میگیرد. معمولا، این بخش توسط مهندسین متخصص با استفاده از نرم افزار ROSA یا WAVE انجام میشود. نرم افزار Reverse Osmosis System Analysis که به اختصار ROSA نامیده میشود یک نرم افزار شبیه سازی برای طراحی آب شیرین کن با فرایند اسمز معکوس می باشد .
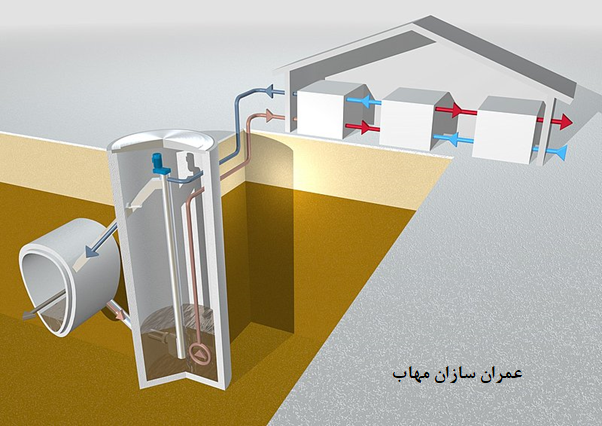
بازیابی استفاده مجدد از پساب Water Treatment Reuse
کاربردهای دستگاه تصفیه صنعتی
- تصفیه آب قبل از ورود به منابع کویل دار، دیگهای بخار، کولینگ تاور ها و تمامی تجهیزات حرارتی و برودتی.
- تصفیه آب شور دریا در مقیاس بسیار بزرگ برای مقاصدی نظیر تامین آب شرب، شستوشو در حمام ها و آشپزخانه بمنظور پخت
- تصفیه آب مورد استفاده در صنایع نفت، گاز و پتروشیمی بمنظور جلوگیری از ورود آب سخت و شور به سیستم ها و ضررهای ناشی از تاثیرات آب شور در تاسیسات نفتی.
- تصفیه نهایی آب پساب خروجی از پکیج تصفیه فاضلاب صنعتی و در حقیقت استفاده مجدد از پساب های صنعتی.
- تصفیه آب کشاورزی برای آبیاری درختان، تامین آب شیرین جهت پرورش آبزیان و تامین آب شیرین برای تولید محصولات غذایی و دارویی.
- تصفیه آبهای خروجی از چاه ها در کارواشها و صنایع وابسته. استفاده مجدد آب بعد از دستگاه تصفیه فاضلاب کارواش.
- تصفیه آب در حد تولید آب مقطر برای انجام دیالیز در مراکز درمانی. در حقیقت تامین آب ورودی به دیونایزر از طریق دستگاه تصفیه آب صنعتی می تواند انجام گیرد.
- استفاده از پکیج اسمز معکوس در صنایع تولید آب معدنی ، کارخانه های تولید آب میوه ، ساندیس
لطفاً جهت کسب اطلاعات بیشتر و مشاوره رایگان با کارشناسان این شرکت تماس حاصل فرمایید.