گرفتگی غشاها در سیستم های اسمز معکوس و راه های مقابله و جلوگیری از آن
رسوبگذاری در غشا یک عیب اجتناب ناپذیر در اسمز معکوس (RO) برای احیای فاضلاب است. به منظور روشن شدن روند گسترش رسوب دهی درغشا، در یک مطالعه تکنیکی و فنی تمامی غشاهای رسوب دار در امتداد کانال خوراک یک سیستم RO در مقیاس صنعتی برای احیای فاضلاب (شش عنصر در هر مرحله) کالبدشکافی و تجزیه و تحلیل شد.
نتایج بدست آمده نشان داد، شار آب و راندمان رد نمک از غشای رسوب زده در سر و انتهای غشا در بین ۱۲ عنصر کمترین بود. گزارش شده عمدتا این رسوب ها از پروتئین ها، پلی ساکاریدها و اسید فولویک تشکیل شده است. غلظت ATP از مواد رساننده بر روی عناصر غشاهای اول و دوازدهم بسیار بیشتر از عناصر دیگر بود، که نشان دهنده سوخت زیستی شدید است. اگرچه میکروب ها به دلیل تولید مواد پلیمری خارج سلولی می توانند باعث رسوب زدگی آلی شوند، اما در این مطالعه هیچ ارتباط روشنی بین رسوب آلی و بیوفولینگ یافت نشد. به عنوان مثال ، اثر غلظت ATP بر روی عنصر دوم و عنصر هفتم مشابه بود، در نتیجه میزان مشابهی از biofouling را نشان داد، اما رسوب آلی عنصر دوم مقایسه با عنصر هفتم نسبتاً کم بود. تقریباً ۷۰٪ از عناصر فلزی، عمدتا Fe ، روی عنصر اول رسوب می کنند. اگرچه غلظت آهن در آب خوراک بسیار کمتر از کلسیم و منیزیم بود، غلظت آهن در سه عنصر اول به طور قابل توجهی بالاتر از هر عنصر دیگر بود ، که نشان می دهد آهن با سهولت بیشتری بر روی غشاهای RO رسوب می کند.
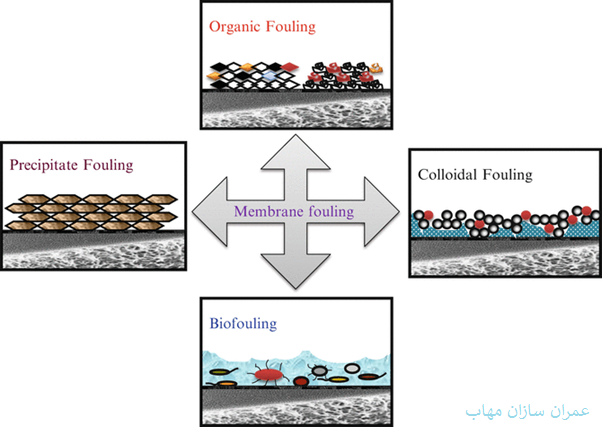
CIP رسوب گرفتگی ممبران اسمز معکوسRO عمران سازان مهاب
روش های پاکسازی غشا در RO
در یک بررسی دیگر، رسوب زدایی و تمیز کردن غشا در سه واحد اسمز معکوس (RO) مورد مطالعه قرار گرفت. این نمونه ها شامل آب خوراک پساب فاضلاب ثانویه، آب رودخانه و آب سطحی بود. کالبد شکافی غشایی برای خصوصیات رسوب استفاده شد. اندازه گیری لایه های فاولینگ شامل کل کربن آلی (TOC) ، آدنوزین تری فسفات، پلی ساکاریدها، پروتئین ها و صفحات هتروتروف بود. در همه مکان ها، رسوبگذاری غشا و اسپیسر (بیو) آلی بود. روش های تمیز کردن استاندارد با دو روش تمیز کردن که به طور خاص برای حذف (بیو) رسوب آلی با استفاده از پاک کننده های ترکیبی تجاری (مخلوط مواد فعال) سازگار شده است، مقایسه شد. سه سیستم RO تحت تأثیر رسوبات غیر قابل برگشت قرار گرفتند که باعث کاهش دائمی عملکرد در افت فشار نرمال و نفوذ پذیری آب حتی پس از تمیز کردن کامل شیمیایی می شود. نتایج نشان داد روش های تمیزکاری ، میانگین TOC را با حداکثر ۸۰ ~ به میزان ۴۵٪ کاهش داد. به طور کلی ، با روش انطباق یافته I در مقایسه با روش تطبیق یافته II ، می توان ۲۰ درصد حذف زیست توده بالاتر را به دست آورد. اندازه گیری های TOC و SEM نشان داد که هیچ یک از روش های تمیزکاری اعمال شده نمی تواند مواد گل آلوده را به طور کامل از عناصر غشا پاک کند. این مطالعه بر نیاز به روشهای تمیز کردن جدید برای هدف قرار دادن رسوبات مقاوم تأکید دارد ، زیرا هیچ یک از روشهای اعمال شده منجر به بازسازی غشای بسیار موثر نمی شود.
استفاده از روش CIP در پاکسازی غشاهای سیستم RO
یکی از مهمترین نگرانیهای مربوط به عملکرد RO ، کاهش عملکرد غشا توسط رسوب است. بیوفولینگ، رایج ترین نوع رسوب زدگی غشایی، نوعی رسوب گذاری است که کنترل آن سخت تر است. افزایش افت فشار کانال تغذیه نرمال (NPD) بر روی کانال فاصله دهنده تغذیه، کاهش نفوذ پذیری آب نرمال شده ویا تغییر در احتباس نمک از شاخص های اصلی عملکرد کلیدی عملیاتی است که توسعه رسوب در برنامه های کاربردی در مقیاس کامل را نشان می دهد. بیوفولینگ سریع به طور معمول در ماژول های مرحله اول آشکار می شود، که باعث افزایش شدید NPD شود، در حالی که بیوفولینگ آهسته ممکن است در کل واحد آشکار شود. به ندرت ، سوخت زیستی در سایر قسمتهای نصب مانند آخرین المان ها مشاهده می شود.
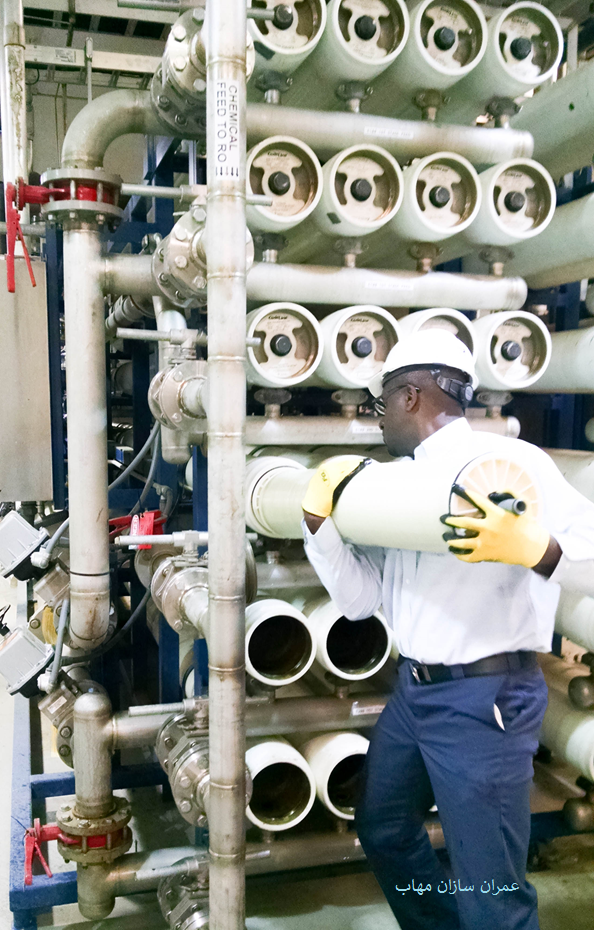
برای غلبه بر مشکلات رسوب، تمیز کردن شیمیایی در محل (CIP)
برای غلبه بر مشکلات رسوب، تمیز کردن شیمیایی در محل (CIP) برای بازگرداندن عملکرد اصلی RO از نظر NPD و ظرفیت رد نمک نرمال اعمال می شود. به طور کلی CIP های اسیدی-بازی اغلب قادر به بازیابی کامل عملکرد RO و حذف تمام رسوبات از عناصر غشا نیستند. اگر عملکرد غشا تا یک سطح مشخص تعریف شده قابل بازیابی نباشد ، کارخانه RO بطور مداوم با مشکلات رسوب کار می کند.
CIP برای صنعت غشا اجتناب ناپذیر است. هزینه های تمیز کردن عناصر غشایی می تواند تا ۵۰٪ از کل هزینه های عملیاتی RO را اضافه کند. بازده CIP شدیداً به واکنشهای شیمیایی بین رسوبات و سطح غشا و همچنین واکنشهای بین مواد رساننده و مواد شیمیایی بستگی دارد که شامل هیدرولیز، پپتیزاسیون، صابون سازی، محلول سازی، پراکندگی و کلاته می شود. دسته های مختلفی از عوامل تمیز کنندگی مانند محلول های قلیایی، اسیدها، مواد شیمیایی فلزات، سورفاکتانت ها، آنزیم ها و عوامل اکسید کننده وجود دارد. علاوه بر این، ترکیبات تجاری فعال مواد شیمیایی در دسترس است، اما تولید کنندگان اغلب ترکیب دقیق را نشان نمی دهند. عوامل تمیز کننده شیمیایی به طور خاص عمل می کنند و انتخاب روش CIP باید به ترکیب رسوب دهی منفرد بستگی داشته باشد. به عنوان مثال محلولهای قلیایی، از طریق هیدرولیز و محلول سازی پی در پی، مواد نسبی آلی موجود در غشا را از بین می برد. عوامل کیلیت فلزی به طور خاص کاتیون های دو ظرفیتی را از مولکول های پیچیده (به عنوان مثال ، مواد پلیمری خارج سلول) حذف می کنند و به همین ترتیب یکپارچگی ساختاری ماتریس لایه رسوب را تضعیف می کنند. سورفاکتانت ها با تشکیل میسل در اطراف آنها، ماکرومولکول ها را حل می کنند و در نتیجه حذف پلان ها از سطح غشا را تسهیل می کنند. تمیز کردن با اسید مشکل پوسته پوسته شدن را حل می کند و یکپارچگی دیواره سلولی میکروارگانیسم ها را از بین می برد و پروتئین ها را رسوب می دهد. عوامل اکسید کننده، مانند پراکسید هیدروژن، قادر به اکسید کردن مواد آلی طبیعی (NOM) هستند و به عنوان بیوسید عمل می کنند و می توانند با افزایش مقدار گروههای عملکردی حاوی اکسیژن مانند گروههای کربوکسیل و فنلی، آب دوستی را افزایش دهند.
پارامترهای عملیاتی مانند مدت زمان ، دما ، تنش برشی و فشار نیز تأثیر قابل توجهی بر کارایی تمیز کردن دارند. چرخه های فیلتراسیون کوتاه (به عنوان مثال ، روش تمیز کردن مکرر اما کوتاه تر) مفید هستند، زیرا لایه های رسوب باگذشت زمان جمع و جورتر می شوند و برداشتن آنها دشوارتر می شود. به طور کلی، کارایی تمیز کردن با افزایش دما افزایش می یابد، اما تحمل گرما در غشا باید در نظر گرفته شود. به نظر می رسد که مواد جداکننده خوراک در غشاهای مارپیچی ، کارایی حذف فولانت را محدود می کند. به هر حال، در صورت وجود یک واکنش شیمیایی مطلوب بین ماده تمیز کننده و پاک کننده ، بهینه سازی شرایط تمیز کردن مانند دما ، pH ، مدت زمان تمیز کردن و سرعت می تواند منجر به افزایش بازده CIP شود.
روش های کنترل رسوب در غشاهای اسمز معکوس
CIP همچنان یکی از گلوگاه های مهم در عملکرد پایدار کارخانه های تمام عیار RO است. بنابراین، اجتناب از سوخت زیستی عامل بسیار مهمی در یک رویکرد موثر پیشگیری و کنترل رسوب است. پیشگیری از بیوفولینگ ممکن است با استفاده از پیش تصفیه بیش از حد یا استفاده از بیوسیدها حاصل شود. با این حال، تنها مواد فعال زیست کش که به طور رسمی توسط اکثر تولید کنندگان RO تأیید می شوند، به ۲،۲-دیبرومو-۳-نیتریلوپروپیونامید (DBNPA) و کلرومتتیلیوزوتیزولون / متیلیزوتیازازولون (CMIT / MIT) محدود می شوند. بیوسیدها و همچنین مواد شیمیایی تمیز کننده باید با تمام مواد یک عنصر RO سازگاری کامل داشته باشند و باید سریع عمل کنند. بیوسیدهای باند پهن با ویژگی های پراکندگی بیوفیلم (به عنوان مثال ، دی اکسید کلر) ممکن است گزینه های امیدوار کننده ای باشند اما هیچ تأیید رسمی از تولید کنندگان غشا ندارند.
استفاده از روش ترکیبی مکانیکی – شیمیایی در تمیز کردن غشاها
با توجه به اینکه CIP های اسید و باز سنتی نتوانستند به طور کامل عملکرد RO را بازیابی کنند و تمام رسوبات را از عناصر غشا پاک کنند. رویکردهای جایگزینی روش های ترکیبی بجای CIP کلاسیک، مانند تمیز کردن دو فازی، پیش از بکارگیری باید عمیق تر مورد بررسی و تأیید سازندگان غشا قرار گیرد، زیرا اعتقاد بر این است که ترکیب تمیز کردن شیمیایی و تمیز کردن مکانیکی، کارایی CIP را بهبود می بخشد. علاوه بر این، تحقیق و توسعه باید بر روی پیشرفت در ساخت عناصر غشایی و ساخت و طراحی غشاهای RO با مقاومت شیمیایی بهبود یافته در برابر اکسید کننده های سموم و سایر مواد شیمیایی فعال مورد استفاده جهت کنترل و پبشگیری از تجمع رسوب متمرکز شود.
آزمایش های تمیز کردن مقایسه ای انجام شده در یک آزمایشگاه نشان دادکه حتی با استفاده از روش های خاص رسوب زدایی بیولوژیکی (آلی) ، رسوب های آلی پیر و مداوم (زیستی) به طور کامل از سطح غشا و فاصله دهنده های غشا پاک نشده اند. سلول های جریان متقابل می توانند ابزاری مفید برای آزمایش مقایسه ای مواد شیمیایی تمیز کننده و روش های CIP باشند، زیرا نمایشی مناسب از فعل و انفعالات فیزیکی پیچیده در طول CIP را ارائه می دهند. از تنظیمات آزمایشگاهی می توان برای دستیابی به پارامترهای مهم CIP مانند حذف فولانت یا یکپارچگی غشا استفاده کرد.
مشکل پوسته پوسته شدن
پوسته پوسته شدن به معنای رسوب ذرات بر روی یک غشا و چسبیدن به آن است. این یک اثر ناخواسته است که می تواند در طی فرآیند های فیلتراسیون نانو و اسمز معکوس رخ دهد. اسکالینگ باعث استفاده بیشتر از انرژی و طول عمر کوتاهتر غشاها می شود، زیرا این موارد بیشتر به تمیز کردن نیاز دارند.
فیلتراسیون نانو و اسمز معکوس فرایندهایی هستند که اغلب برای تهیه آب آشامیدنی از آبهای زیرزمینی یا سطحی استفاده می شوند. در طی این فرآیندها یک حجم تبدیل بالا مورد نظر است، زیرا این امر باعث کاهش اتلاف مواد اولیه و انرژی می شود. حدود ۷۵ تا ۹۰ درصد آب خوراک در این نوع فرایندها به محصول مورد نظر تبدیل می شود. در طی فرآیند، کنسانتره غشایی نمک ها را جذب می کند. نمکهای غیرآلی، مانند کربنات کلسیم و سولفات باریم، که در آب محلول نیستند، می توانند بیش از حد اشباع شوند. این باعث رسوب آنها می شود. احتمال افزایش نمک های محلول در آب در غشا در چنین حالتی هنگام تبدیل زیاد است.
همچنین اسکالینگ باعث کاهش شار اسمی می شود. از پیامد های این پدیده استفاده بیشتر از انرژی، افزایش دوره تناوب تمیز کردن و طول عمر کوتاهتر غشاها است. این امر باعث می شود که فرآیند تصفیه آب غشایی بسیار گران شود. افزودن اسیدها یا مواد ضد رسوب به سیستم می تواند از رسوب نمک جلوگیری کند. اسیدها اشباع بیش از حد کربنات کلسیم را کاهش می دهند. یک واحد فیلتراسیون غشایی در حداکثر تبدیل و حداقل دوز اسیدها و ضد مقیاس، بدون وقوع پوسته پوسته شدن ، عملکرد بهینه ای دارد.
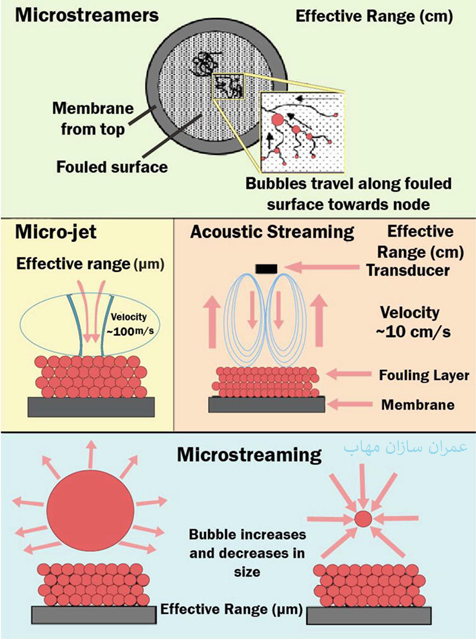
برای غلبه بر مشکلات رسوب، تمیز کردن شیمیایی در محل (CIP)
بیوفولینگ
آلودگی بیولوژیکی، معروف به سوخت زیستی، اغلب در طی فرآیند های فیلتراسیون نانو و اسمز معکوس رخ می دهد. دلیل این امر آن است که غشاها با کلر ضد عفونی نمی شوند تا باکتری ها از بین بروند. سوخت زیستی در غشا های تصفیه نانو یا اسمز معکوس احتمالاً کمترین آلودگی قابل درک در سیستمهای غشایی است. این را می توان به رشد پیچیده باکتری ها نسبت داد. اثرات مخرب این میکروارگانیسم ها، بر روی فیلترهای نانو و سیستم های اسمز معکوس غالباً غیرقابل جبران می باشد.
انواع میکروارگانیسم ها، فاکتورهای رشد و غلظت آنها در یک سیستم غشایی به شدت به عوامل حیاتی مانند دما، وجود نور خورشید ، pH ، غلظت اکسیژن محلول و وجود مواد مغذی آلی و غیر آلی بستگی دارد. این میکروارگانیسم ها می توانند از طریق آب یا هوا یا هر دو وارد سیستم شوند. باکتری های هوازی معمولاً در محیطی با آب گرم، کم عمق و در معرض خورشید، با محتوای اکسیژن محلول زیاد و اسیدیته ۶.۵ تا ۸.۵ و مقدار زیادی مواد مغذی آلی و معدنی زندگی می کنند.
همانطورکه جریان پرمیت از طریق غشا خارج می شود، تمام ناخالصی ها در نزدیکی سطح غشا باقی می مانند. لایه آب کنار سطح غشا (لایه مرزی) به طور فزاینده ای در مواد محلول و معلق متمرکز می شود. این غلظت ها بسته به سرعت تغذیه، بازیابی عناصر و شار نفوذ غشا به یک سطح ثابت خاص می رسند.
رعایت توصیه های سازنده غشا در مورد حداقل جریان تغذیه، حداکثر بازیابی عنصر و حداکثر شار عنصر مهم است. این توصیه ها بر اساس اندازه عنصر و کیفیت آب خوراک تصفیه شده است. غلظت مواد جامد محلول و معلق در لایه مرزی عملکرد غشا را کنترل می کند. غلظت های بالاتر به معنی فشار اسمزی بالاتر، تمایل بیشتر مواد معلق به لخته شدن و پوشاندن سطح غشا و احتمال وقوع پوسته پوسته شدن بیشتر است. حفظ شرایط عملیاتی مناسب برای غشا گام اصلی پیشگیری برای به حداقل رساندن رسوب گذاری غشا است. پوسته پوسته شدن به معنای رسوب ذرات بر روی یک غشا و وصل شدن آن است. این یک اثر ناخواسته است که می تواند در طی فیلتراسیون نانو و فرآیندهای اسمز معکوس رخ دهد. مقیاس گذاری باعث استفاده بیشتر از انرژی و طول عمر کوتاهتر غشاها می شود، زیرا این موارد بیشتر به تمیز کردن نیاز دارند. فیلتراسیون نانو و اسمز معکوس فرایندهایی هستند که اغلب برای تهیه آب آشامیدنی از آبهای زیرزمینی یا سطحی استفاده می شوند. در طی این فرآیندها یک تبدیل بالا مورد نظر است، زیرا این امر باعث کاهش اتلاف مواد اولیه و انرژی می شود. در طی فرآیند، کنسانتره غشایی نمک ها را جذب می کند. نمک های غیرآلی ، مانند کربنات کلسیم و سولفات باریم، که در آب محلول نیستند، می توانند بیش از حد اشباع شوند. این باعث رسوب آنها می شود. احتمال افزایش نمک های محلول در آب در غشا هنگام تبدیل زیاد است.
مقیاس گذاری باعث کاهش شار اسمی نیز می شود. همانطور که قبلاً اشاره شد، استفاده بیشتر از انرژی، افزایش فرکانس تمیز کردن دلیل طول عمر کوتاهتر غشاها است. این امر باعث می شود فرآیند تصفیه آب غشایی بسیار گران شود. افزودن اسیدها یا مواد ضد رسوب به سیستم می تواند از رسوب نمک جلوگیری کند. اسیدها اشباع بیش از حد کربنات کلسیم را کاهش می دهند، در حالی که ضد رسوبات میزان فولینگ را کاهش می دهند. یک واحد فیلتراسیون غشایی در حداکثر تبدیل و حداقل دوز اسیدها و ضد رسوبات ، بدون وقوع پوسته پوسته شدن ، عملکرد بهینه ای دارد.
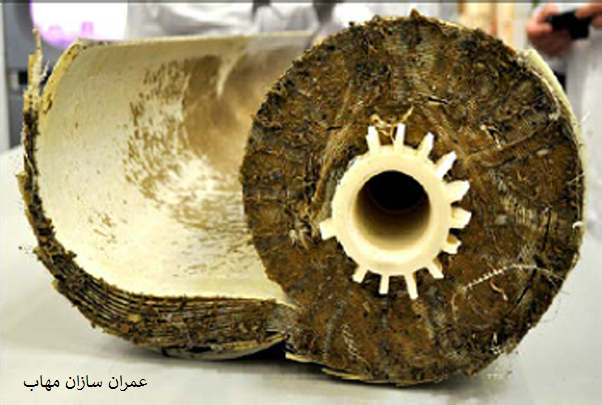
CIP رسوب گرفتگی ممبران اسمز معکوسRO عمران سازان مهاب
بیوفولینگ
آلودگی بیولوژیکی، معروف به سوخت زیستی ، اغلب در طی فرآیند های فیلتراسیون نانو و اسمز معکوس رخ می دهد. دلیل این امر آنست که غشاها با کلر ضد عفونی نمی شوند تا باکتری ها از بین بروند. سوخت زیستی در غشاهای تصفیه نانو یا اسمز معکوس احتمالاً کمترین آلودگی قابل درک در سیستمهای غشایی است. این را می توان به رشد پیچیده باکتری های میکروبیولوژیک نسبت داد. این میکروارگانیسم ها اثرات مخرب، غالباً غیرقابل جبرانی بر روی فیلترهای نانو و سیستم های اسمز معکوس دارند.
انواع میکروارگانیسم ها ، فاکتورهای رشد و غلظت آنها در سیستم غشایی به شدت به عوامل حیاتی، از جمله دما، وجود نور خورشید ، pH ، غلظت اکسیژن محلول و وجود مواد مغذی آلی و غیر آلی بستگی دارد. میکروارگانیسم ها می توانند از طریق آب یا هوا یا هر دو وارد سیستم شوند. باکتری های هوازی معمولاً در محیطی با آب گرم، کم عمق و در معرض خورشید، با محتوای اکسیژن محلول بالا، pH 8.5 تا ۶.۵ و مقدار زیادی مواد مغذی آلی و معدنی زندگی می کنند. از طرف دیگر، باکتریهای بی هوازی معمولاً در سیستمهای بسته با اکسیژن محلول کم وجود دارند و در صورت وجود مقدار کافی مواد مغذی فعال می شوند. هر دو نوع باکتری می توانند در یک سیستم وجود داشته باشند. باکتری هایی وجود دارند که می توانند بین شرایط هوازی و هوازی جابجا شوند و بالعکس. ماهیت آنها به وضعیت آب بستگی دارد.
یکی از فراوانترین انواع سوختهای زیستی در طی پیش تصفیه سیستمهای اسمز معکوس و در قسمتهایی از سیستمهای غشایی ایجاد می شود که می تواند رشد جلبکها را تقویت کند. قطعات سیستم غشایی که در معرض نور خورشید هستند یا حاوی آب ساکن هستند می توانند باعث گسترش رشد جلبک ها شوند.
نور خورشید نقش مهمی در روند فتوسنتز برای رشد جلبک ها دارد. میزان نور خورشید میزان اکسیژن تولید شده را تعیین می کند. باکتری های هوازی که وابسته به اکسیژن هستند ، وقتی اکسیژن محلول در آب خوراک به مقدار لازم برای انجام متابولیسم کافی نباشد، به اکسیژن تولید شده توسط جلبک ها نیاز دارند. در حالی که جلبک ها از بین می روند، آنها به یک منبع غذایی برای باکتری ها تبدیل می شوند، زیرا مواد مغذی آلی را که باکتری ها برای رشد در سیستم غشایی نیاز دارند آزاد می کنند.
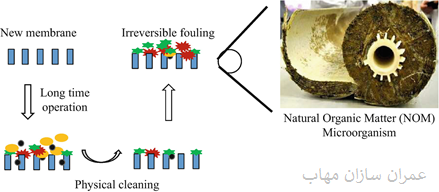
CIP رسوب گرفتگی ممبران اسمز معکوسRO عمران سازان مهاب
نوع دیگر سوخت زیستی در سیستم غشایی، اتصال باکتری ها به دیواره های داخلی خطوط لوله است. گوشه ها و بن بست ها مکان هایی در یک خط لوله هستند که باکتری ها می توانند به آنها جذب شوند. پس از جذب باکتری ها به دیواره، اولین قسمت های یک فیلم زیستی تشکیل می شود. در حالی که باکتری ها همچنان تکثیر می شوند و مواد آلی مرده به ساختارهای فیلم بیو جذب می شوند، اندازه این فیلم زیستی افزایش می یابد. علی رغم این واقعیت که فیلم های زیستی جریان آب را تحت تأثیر قرار می دهند، هنوز هم مواد معلق کوچک و میکروارگانیسم ها را به خود جلب می کند. رسوبات فیلم زیستی به یک بستر منسجم و قوی تبدیل می شود که حذف آن بسیار سخت است. در نهایت ، بخشهایی از فیلم زیستی آزاد و از طریق اجزای سیستم، از جمله غشاها پخش می شود. هنگامی که آنها به غشا متصل می شوند، میکروارگانیسم ها با استفاده از مواد مغذی موجود در آب خام ورودی، شروع به تکثیر می کنند. در نتیجه یک فیلم زیستی بر روی غشاها ایجاد می شود که جریان آب خوراک را از طریق غشا مسدود می کند. این منجر به فشار بالاتر می شود، که باعث افزایش هزینه های سیستم و آسیب جبران ناپذیر به غشاها می شود.
حتی این اتفاق می افتد که برخی از مواد غشایی محیط مناسبی برای رشد میکروارگانیسم ها هستند، که باعث می شود غشا در مدت زمان کوتاهی به طور کامل از بین برود. از طرف دیگر، باکتریهای بی هوازی معمولاً در سیستمهای بسته با اکسیژن محلول وجود دارند.
رسوبات موثر در کاهش عمر غشاهای RO
رسوب دهی در غشا یک نقص مهم در کاهش کارایی و کاربرد گسترده فناوری اسمز معکوس (RO) است. در یک مطالعه فنی، غشاهای RO در یک کارخانه احیا فاضلاب شهری کالبدشکافی شد. بررسی ها نشان داد که ناخالصی های یونی در کنسانتره RO منجر به پوسته پوسته شدن جدی در غشاهای RO نشد، که با برخی تحقیقات دیگر در تضاد بود. آهن، کلسیم و منیزیم عناصر اصلی غیر آلی هستند. آهن غلظت نسبتاً کمی در نفوذ RO داشت اما بیشترین میزان آن در غشا بود. با این حال، هیچ پیش تصفیه خاصی از نظر حذف آهن وجود نداشت. مقیاس گذاری کلسیم و منیزیم توسط مواد ضد پاششی تزریق شده کنترل شد. رسوب آلی به دلیل مقدار زیادی مواد آلی محلول در پساب ثانویه، مشکل اصلی غشاهای RO بود. کسر اسید آب دوست (HIA ، ۴۸.۰٪ از کل DOC)، اسید آبگریز (HOA ، ۲۳.۶٪) و کسر خنثی آبگریز (HON ، ۱۹.۰٪) کسر بزرگترین در میان شش بخش در ورودی RO بودند.
انواع رسوب غشایی
آلودگی غشایی هنگامی رخ می دهد که آلودگی ها در سطح یا منافذ غشای فیلتراسیون جمع شوند. فولانت ها جریان آب را از طریق غشا محدود می کنند، در نتیجه عواقب مختلفی از جمله مقاومت هیدرولیکی بالاتر، مصرف انرژی بیشتر و حتی آسیب رساندن به غشا و سایر اجزای سیستم ایجاد می شود. انواع رسوب زدایی غالباً با توجه به نوع رسوبات موجود در جریان تغذیه ای تعریف می شود که می تواند شامل رسوب ذرات معلق / کلوئیدی ، رسوب بیولوژیکی / میکروبی و رسوب آلی باشد. هر یک از این انواع رسوب گذاری می تواند برگشت پذیر باشد. مثلاً وقتی پلانت ها از نظر شیمیایی با مواد غشایی پیوند می خورند و عملکرد آن را به طور دائمی به خطر می اندازند . انواع عمده مواد آلاینده غشایی عبارتند از :
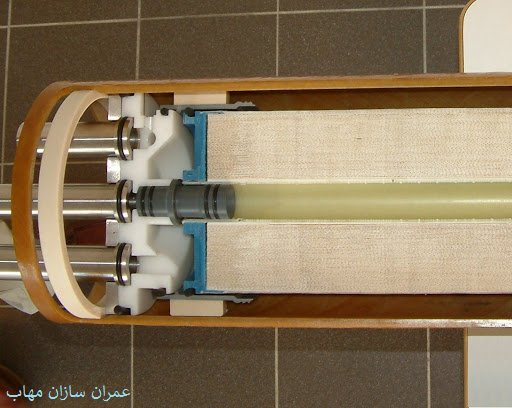
CIP رسوب گرفتگی ممبران اسمز معکوسRO عمران سازان مهاب
رسوب ذرات و کلوئید
رسوب ذرات هنگامی رخ می دهد که مواد جامد معلق و یا مواد کلوئیدی سوراخ های یک غشا را مسدود یا به سطح آن بچسبند. با جمع شدن ذرات بر روی غشا، ، آنها به عنوان لایه “کیک” شناخته می شوند که مانع جریان آب در منافذ غشا می شوند و در نتیجه علائمی مانند افزایش اندازه گیری های دیفرانسیل فشار و افزایش مصرف انرژی ایجاد می شود.
رسوب گذاری ذرات معلق / کلوئید به دلیل وجود ذرات غیر بیولوژیکی و غیرآلی (به عنوان مثال سیلت یا خاک رس) در آب خام ورودی ایجاد می شود، به ویژه هنگامی که جریان از یک توده آب سطحی تأمین می شود. برای اندازه گیری خطر نسبی رسوب زدگی ذرات / کلوئید، متخصصان تصفیه آب معمولاً شاخص چگالی سیلت (SDI) یک جریان خوراک را اندازه گیری می کنند. اندازه گیری SDI به ویژه هنگام نصب سیستم های RO بسیار مهم است، زیرا این سیستم ها کوچکترین منافذ را در بین سیستم های فیلتراسیون غشایی دارند و در نتیجه در برابر رسوب ذرات بسیار آسیب پذیر هستند.
رسوب بیولوژیکی و میکروبی
بیوفولینگ فرایندی است که در آن میکروارگانیسم ها، گیاهان، جلبک ها یا سایر آلاینده های بیولوژیکی روی یا درون غشاهای فیلتراسیون و منافذ رشد می کنند. رسوبات بیولوژیکی و میکروبی تمایل به رشد در محیط های گرم با دبی کم دارند، جایی که آنها می توانند به غشا متصل شده و تکثیر شوند، در حالی که ماده محافظی به نام ماده چند سلولی خارج سلول (EPS) آزاد می شود. در مجموع، میکروارگانیسم ها و EPS یک لایه ژل باریک تشکیل می دهند که به عنوان بیوفیلم شناخته می شود. خواص شیمیایی بیوفیلم باعث می شود آن در برابر استراتژی های تمیز کردن طبیعی مانند شستشوی معکوس یا استفاده از بیوسیدها مانند کلر مقاوم باشد. اکسیداسیون غشا، اگرچه ماده خنثی کننده ای نیست، اما بیشتر اوقات در اثر حمله کلر آزاد ایجاد می شود، دائمی است و قابل برگشت نیست.
تصحیح غشای بیوفولد ممکن است چالش برانگیز باشد و در بعضی موارد ممکن است نیاز به تعویض داشته باشد. با گذشت زمان، یک غشای بیوفولد جریان آب را از یک طرف غشا به طرف دیگر محدود می کند، شرایطی که به شکل فشار دیفرانسیل بیشتر از خوراک به سمت جریان غلیظ است، همچنین کاهش شار غشا، فشار بیشتر و بیشتر هزینه های انرژی را سبب می گردد.
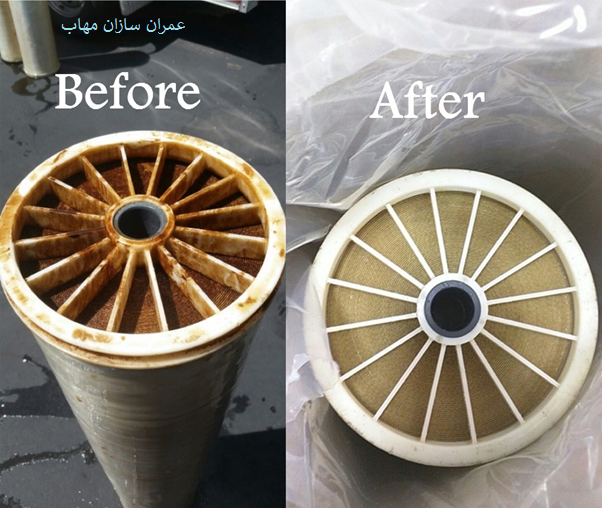
CIP رسوب گرفتگی ممبران اسمز معکوسRO عمران سازان مهاب
رسوب گذاری معدنی و پوسته شدن
پوسته پوسته شدن، همچنین به عنوان رسوب معدنی یا رسوبی شناخته می شود که به دلیل وجود نمک های متبلور، اکسیدها و هیدروکسیدها در محلول خوراک ایجاد می شود. پوسته پوسته شدن غشا زمانی اتفاق می افتد که مواد تشکیل دهنده محلول از محلول رسوب کرده و روی سطح غشا جمع شده و یا در منافذ آن قرار بگیرند. رسوب گذاری بارش هنگامی اتفاق می افتد که یک محلول بیشتر و بیشتر در سمت خوراک غشا متمرکز شود و در نهایت از نقطه اشباع محلول پیشی بگیرد و باعث شود مواد تشکیل دهنده یونی از محلول بیرون بیایند و متبلور شوند و یا به سطح غشا متصل شوند. سیستم های RO / NF با نرخ تبدیل بالا در معرض این خطر ویژه هستند، به ویژه هنگامی که در جریان خوراک غلظت های کلسیم یا منیزیم قابل توجهی داشته باشد.
با استراتژی های درمانی که از رشد کریستال جلوگیری می کنند ، از طریق تزریق اسید ، نرم شدن و استفاده از سایر مهارکننده های مقیاس شیمیایی ، می توان از رسوب معدنی جلوگیری کرد. در حالی که هر یک از این استراتژیها موثر است، باید مراقب بود تا از انتخاب روشهای شیمیایی مغایر با ماده غشایی انتخاب شده جلوگیری شود.
رسوب آلی
رسوب آلی به عنوان مجموعه ای از مواد بر پایه کربن بر روی غشای فیلتراسیون تعریف می شود. مواد آلی طبیعی متشکل از ترکیبات پایه کربن است که معمولاً در خاک، آب های زیرزمینی و سطحی یافت می شود و در نتیجه تجزیه مواد گیاهی و حیوانی است. مواد آلی غالباً کاملاً واکنشی هستند. تاسیسات می توانند با انتخاب ماده غشایی که در برابر جذب مواد آلی به غشا مقاومت می کند، مشکلات مربوط به رسوب زدایی آلی را به حداقل برسانند.