SWRO در حال حاضر شکل غالب تصفیه آب شیرین کن تجاری است. با این حال، انرژی مورد نیاز برای پمپاژ فشار بالا SWRO را به گزینه ای گران قیمت برای تولید آب آشامیدنی در مقایسه با گزینه های رایج مانند تصفیه آب سطحی و IPR تبدیل می کند.
اولین کارخانه بزرگ SWRO شهری در سال 1980 در جده، عربستان سعودی نصب شد. این واحد 8 کیلووات ساعت انرژی به ازای هر متر مکعب آب تولید شده مصرف کرد. این انرژی مصرف شده کمتر از نصف آنچه معمولاً توسط سایر فرآیندهای تقطیر معمولی مصرف می شد، بود. با این حال، فناوری شیرین سازی SWRO یک عیب دارد. آب دریا که قرار است شیرین سازی شود با کمک پمپ های فشار قوی تحت فشار قرار می گیرد. در طی این فرآیند مقدار زیادی انرژی مصرف می شود. پس از اتمام نمک زدایی، باقیمانده آب رد شده باید به عنوان زباله از بین برود. از آنجا که رد کردن آب نمک در این فرآیند فشار زیادی دارد، صرفاً ریختن آن به دریا اتلاف انرژی است. از این فشار می توان دوباره استفاده کرد و بنابراین می توان انرژی را بازیافت کرد. این ایده منجر به نوآوری دستگاه های بازیابی انرژی (ERD) شد که از اتلاف انرژی در فرآیند SWRO جلوگیری می کند. انرژی هیدرولیکی موجود در آب نمک رد شده با فشار زیاد را می توان با کمک ERD مورد استفاده مجدد قرار داد و بنابراین می توان مصرف انرژی را با مقادیر زیاد قابل توجهی کاهش داد. توسعه ERD ها در راه اندازی و بهره برداری از نیروگاه های SWRO در مقیاس بزرگ کمک کرده و دوام اقتصادی فرآیند نمک زدایی را تسهیل می کند. انرژی مورد نیاز نیروگاه های SWRO معمولی در حال حاضر به میزان 1.6 کیلووات ساعت در متر مکعب کم است، و این فرایند را نسبت به سایر فن آوری ها مقرون به صرفه تر و کارآمدتر می کند. حدود 80٪ از کل هزینه آب شیرین کن ناشی از مصرف انرژی و استهلاک سرمایه است. هزینه های باقیمانده با سایر عملیات نگهداری مانند جایگزینی غشاها و سایر اجزا، هزینه های مربوط به نیروی کار و غیره همراه است.
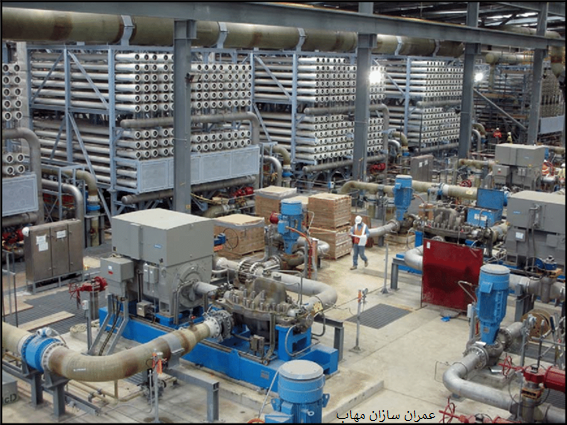
دستگاه های بازیابی انرژی در واحد های SWRO
استفاده از سیستم های ERD در کاهش انرژی مصرفی واحد های SWRO
پمپاژ فشار بالا برای غلبه بر فشار اسمزی موجود در آب خوراک شور به یک جریان کنسانتره شور که بسیار تحت فشار است، نیاز دارد. ERD یا دستگاه های کاهنده انرژی معمولاً برای بازیابی این انرژی هیدرولیکی و انتقال آن به جریان تغذیه استفاده می شود، همچنین از میزان انرژی مورد نیاز نیروگاهها و هم از نیروگاه برق مورد نیاز می کاهد (Guirguis، 2011). اولین ERD های مورد استفاده در کارخانه های SWRO دستگاه هایی از نوع گریز از مرکز مانند Francis Turbine ، Pelton Wheel و Turbocharger بودند (Urrea و همکاران ، 2019). این دستگاه ها انرژی هیدرولیکی کنسانتره را به انرژی مکانیکی تبدیل می کنند تا یک پیستون یا پمپ را هدایت کند، که انرژی هیدرولیکی را دوباره به داخل خوراک منتقل می کند.
از حدود سال 2000 ، ERD های ایزوباریک جایگزین دستگاه های گریز از مرکز در بیشتر کارخانه های مدرن SWRO شده اند. ERD های ایزوباریک انرژی هیدرولیکی را از کنسانتره به طور مستقیم به خوراک منتقل می کنند، زیرا در این سیستم ها دو جریان مستقیم در تماس هستند (با حداقل مخلوط شدن). در نتیجه تبدیل انرژی منفرد، در مقایسه با ERD های گریز از مرکز، افت کارایی کاهش می یابد. دو نوع اصلی از اتاق ایزوباریک وجود دارد: چرخشی و پیستونی:
ERD های چرخشی شامل یک روتور مرکزی است که بر روی یاتاقان هیدرودینامیکی کار می کند که در آن خوراک با فشار کم و کنسانتره با فشار بالا جریان می بایند. روتور با خوراک فشار کم پر می شود، مهر و موم می شود، سپس کنسانتره فشار بالا وارد می شود، خوراک فشار کم را تحت فشار قرار می دهد ، و آن را به سمت غشای RO فشار می دهد. پس از آب بندی مجدد روتور، کنسانتره کم فشار حاصل از آن با تغذیه آب کم فشار ورودی جابجا شده و فرآیند تکرار می شود. (Pressure Exchangeبه دلیل فضای کم، دوام، طراحی مدولار و کارآیی، پرکاربردترین ERD دوار در کارخانه های SWRO مدرن است (Farooque et al.، 2004؛ Kadaj and Bosleman، 2018؛ Urrea et al.، 2019)
ERD های پیستونی فرآیند مشابه تبادل انرژی هیدرولیکی را دنبال می کنند، با انتقال انرژی بین کنسانتره و خوراک در داخل سیلندرهای هیدرولیک، با فرایند فشار متناوب / فشارزدایی متناوب وجود دارد که توسط دریچه های سوئیچ کنترل می شود. ERD های پیستونی نسبت به دستگاه های PX کم حجم و مدولار هستند و به دلیل نیاز به محرک های کنترل و شیرآلات به هزینه و نگهداری سرمایه بالاتری نیاز دارند (Guirguis، 2011).
بازده ERD (که عبارتست از تغییر در فشار جریان خوراک تقسیم بر تغییر در فشار کنسانتره) برای ERD های مختلف مشخص شده است که توربین 75٪ ، توربوشارژ 80٪ است، در حالی که اتاق های ایزوباریک حدود 95-97٪ هستند (کیم و همکاران ، 2019 ؛ Urrea و همکاران ، 2019). SEC برای نیروگاه های SWRO که در آن ERD های مختلف نصب شده است، گزارش شده است: توربین های Francis> 6 کیلووات ساعت در متر مکعب 3 ، چرخ های Pelton 3.5-5.9 کیلووات ساعت در متر مکعب 3 ، ERD های پیستون محور 3.5-4.6 کیلووات ساعت در متر مکعب 3 و PX.3 ۵ کیلووات ساعت در متر مکعب. PX در میزان بهبودی حداکثر تا 50٪ موثر است (Urrea و همکاران ، 2019). صرفه جویی در مصرف انرژی با بکارگیری سیستم ERD در مقایسه با سیستم های استاندارد SWRO می تواند در محدوده 25-40٪ باشد (Peñate و García-Rodríguez، 2011).
ERD های دوار مانند PX معمولاً به دلیل فشردگی و دوام دستگاه ترجیح داده می شوند، و با بازده 95-97٪ ، کار می کنند. پیشرفت های عمده در زمینه تولید ERD ها به حدی است که اکنون در کارخانه های SWRO امری عادی است و جدیدترین دستگاه های (ایزوباریک) با بازده 97٪ کار می کنند و به برخی از نیروگاه ها امکان دستیابی به ثبات 3 کیلووات ساعت در متر مکعب را می دهد و 10 برابر معمول تصفیه آب سطحی است. اگرچه ERD برای کارآمدتر و مقرون به صرفه تر کردن انرژی SWRO ضروری است، اما پیشرفت های آینده در فناوری ERD مزایای محدودی در کاهش بیشتر مصرف انرژی SWRO ایجاد می کند.
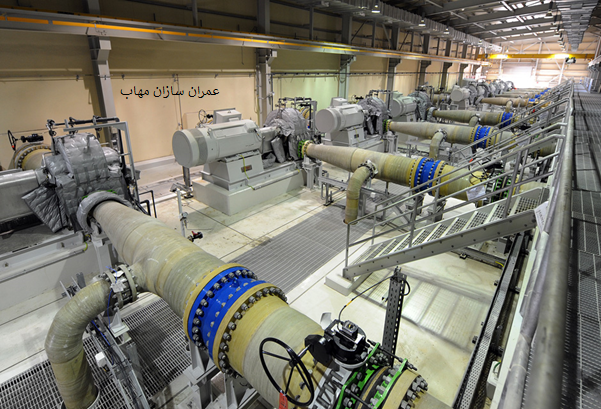
دستگاه های بازیابی انرژی در واحد های SWRO
پیکربندی فرآیند RO در راستای کاهش مصرف انرژی
چندین پیکربندی فرآیند SWRO برای دستیابی به پیشرفتهایی در بهره وری انرژی و کیفیت آب تولید شده است.
Single pass RO یا اسمز معکوس تک پاس(شکل 1A) به دلیل سادگی، سهولت کارکرد و نسبتاً کم هزینه ، پیکربندی متداول و گسترده است. اسمز معکوس تک گذر با غلظت TDS بین 300 تا 500 میلی گرم بر لیتر نفوذ می کند و سرعت بهبودی آن تا 50 درصد است (Kim and Hong، 2018). در صورت نیاز به آب محصول با کیفیت بالاتر، ممکن است گذرگاه RO اضافی مورد نیاز باشد.
RO با دو پاس شامل یک واحد RO دوم به صورت سری است که برای رسیدن به کیفیت بهتر، جریان پرمیت از واحد اول را تصفیه می کند. انرژی اضافی (و هزینه) مورد نیاز برای اجرای RO دوم این گزینه را به طور کلی غیرقابل اجرا می کند (غفور و همکاران ، 2015).
RO با دو گذر /پاس جزئی (شکل 1 B) شامل تغذیه بخشی از نفوذ عبور اول از طریق RO دوم است ، در حالی که نفوذ باقیمانده RO را دور می زند و با نفوذ عبور دوم ترکیب می شود. SEC به نسبت جریان پرمیت تصفیه شده و عبور داده شده به نفوذ بستگی دارد (Du et al.، 2015). مطالعات نشان داده است که RO با یک گذر به طور کلی انرژی کمتری نسبت به گزینه های مختلف RO برای دو پاس نیاز دارد. در صورتي كه استانداردهاي كيفيت آب محصول از سختگيري بيشتري برخوردار باشد، به گذرگاه دوم نياز است. برای دو پیکربندی گذر RO مشخص شد که Spit Partial Second Pass RO کمترین انرژی را مصرف می کند. با این حال اشاره شده است که این یافته ها تنها نشان می دهد که چگونه می توان نیروگاه های SWRO را در محدوده گزارش شده در حال حاضر SEC بهینه سازی کرد.
گزارش شده است كه SSP باعث كاهش رسوب و افزايش عملكرد SWRO و همچنين كاهش مصرف انرژي و بهبود كيفيت نفوذ تا 15٪ در مقايسه با تك گذر معمولي مي شود (وارسينگر و همكاران ، 2016). با SPSP ، پرمیت فوروارد (TDS پایین) RO از گذر دوم عبور می کند، در حالی که جریان پرمیت بک وارد به گذرگاه دوم تغذیه می شود، پس از آن دو جریان پرمیت مخلوط می شوند. گزارش شده است که SPSP کمترین SEC را از دو تنظیمات عبور دارد (Du et al.، 2015). تنظیمات اضافی RO شامل عبور کنسانتره RO از واحد RO دیگر برای دستیابی به افزایش بازیابی وکاهش حجم کنسانتره، کاهش نیاز به اندازه واحد طراحی شده است. با این حال، SEC به دلیل فشار زیاد مورد نیاز در پاس دوم افزایش می یابد (Du et al.، 2015).
صرفه جویی در مصرف انرژی همچنین می تواند با گروه بندی اجزای کارخانه RO در سه بانک (خوراک فشار بالا؛ غشا؛ ؛ بازیابی انرژی)، که به عنوان “سه مرکز RO” شناخته می شود، به دست آید. این پیکربندی در کارخانه های بزرگ RO در استرالیا، اسرائیل وخاورمیانه به کار گرفته شده وتقاضای انرژی برای جریان های روزانه را کاهش می دهد (Voutchkov، 2018). با این وجود، در صورتی که SWRO فقط بخش کوچکی از تقاضای کل را تأمین کند، بنابراین برای کار در حالت دسته ای (جریان ثابت)، مانند مراکز آب شیرین کن که برای تکمیل منابع آب شیرین موجود استفاده می شود، سه مرکز طراحی فایده ای نخواهد داشت.
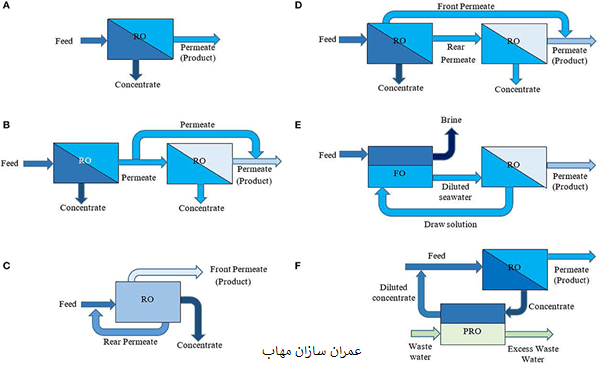
دستگاه های بازیابی انرژی در واحد های SWRO
تنظیمات فرآیند ترکیبی
ادغام فناوری های شامل RO به خوبی تثبیت شده است. فن آوری های در حال ظهور مانند اسمز عقب مانده فشار (PRO) و اسمز رو به جلو (FO) برای بهینه سازی نمک زدایی آب دریا، کانون تحقیقات بسیاری بوده است (عواد و همکاران، 2019). PRO و FO هر دو با وارد كردن جریان پساب رقیق تر به فرآیند، برنامه های بالقوه ای در نمك زدایی SWRO دارند.
اسمز جلو یا فورارد اسمز
FO شامل انتقال غیرفعال مولکول های آب از طریق غشایی نیمه تراوا از خوراک رقیق تر به محلول کم رقت است. FO به جای وارد کردن فشار هیدرولیکی برای هدایت آب در جهت مخالف، به شیب فشار اسمزی بین دو محلول متکی است. محلول رقیق برای بازیابی آب شیرین را از محلول غلیظ تحت تصفیه می گیرد. غشاهای FO در مقایسه با RO تحت فشار هیدرولیکی کم و بدون فشار کار می کنند، بنابراین باعث کاهش مصرف انرژی می شوند. عدم پمپاژ منجر به کاهش تعلیق ذرات جامد می شود که احتمال رسوب زدگی را کاهش می دهد (Valladares Linares et al.، 2014؛ Awad et al.، 2019).
یک مانع عمده در برابر FO بازیابی محلول بسیار غلیظ و نیاز به انرژی مرتبط است (عواد و همکاران ، 2019). همچنین به تولید غشای دفع کننده نمک زیاد و شار بالا نیاز دارد (Valladares Linares و همکاران، 2014). غشاهای RO معمولی به دلیل قطبی شدن بالای غلظت ناشی از غلظت زیاد محلول، که می تواند منجر به رسوب زدایی غیر آلی شود، برای FO نامناسب هستند (Zheng، 2017). محلول غلیظ باید با دقت انتخاب شود تا اطمینان حاصل شود که غلظت و فشار اسمزی از خوراک بالاتر است و به گونه ای است که می توان آب شیرین را به راحتی از محلول کشش بازیابی کرد.
اگرچه استفاده از FO با نمک زدایی SWRO هنوز نتوانسته است به سودآوری تجاری دست یابد (Altaee et al.، 2018؛ Awad et al.، 2019 ، FO می تواند به عنوان پیش تصفیه نمک زدایی SWRO مورد استفاده قرار گیرد، با پتانسیل کاهش مصرف انرژی نرخ بازیابی را در مقایسه با فرآیندهای معمولی SWRO افزایش دهید.
غشای FO بسیار انتخابی، همراه با فرآیند بازیابی و بازسازی محلول کشش، خلوص محلول کشش را حفظ می کند. این میزان رسوب گذاری غشای RO را که تحت فشارهای هیدرولیکی بالایی است به حداقل می رساند و در غیر این صورت از کاهش شار و افزایش پمپاژ و انرژی ناشی از آن آسیب می بیند (Altaee et al.، 2018). رسوب کاهش یافته نیز به افزایش عمر غشا کمک می کند. برخی از اشکالات پیش تصفیه شامل هزینه سرمایه اضافی برای پمپاژ غشای اضافی (FO) و مواد شیمیایی مورد نیاز در مقایسه با RO معمولی است. مطالعات قبلی نشان داده است که مصرف انرژی برای شوری آب دریا زیر 35 گرم بر لیتر مطلوب نیست و FO فقط در صورت نصب ناکارآمد یا عدم استفاده از ERD می تواند باعث کاهش انرژی شود (Altaee et al.، 2018).
مزیت اصلی روش FO-RO این است که برای هدایت خوراک از طریق غشا RO به انرژی هیدرولیکی کمتری نیاز است. یکی از اصلی ترین اشکال ها وجود یک خوراک FO با غلظت کم مانند پساب تصفیه شده است که ممکن است با محل قرارگیری نمک زدایی در محل تصفیه خانه فاضلاب حاصل شود.

دستگاه های بازیابی انرژی در واحد های SWRO
اسمز عقب مانده فشار PRO
فناوری PRO اولین بار در دهه 1970 در اسرائیل توسعه یافت (ساکای و همکاران ، 2016)، در ابتدا به عنوان یک فناوری تولید انرژی با استفاده از آب دریا، بدون آب شیرین کن RO راه اندازی شد. اولین نیروگاه عملیاتی PRO در نروژ آغاز به کار کرد، اما این نیروگاه در سال 2014 به دلیل عملکرد نامطلوب تعطیل شد (Altaee et al.، 2017).
PRO را می توان به عنوان RO-PRO در فرآیند SWRO ادغام کرد. کنسانتره RO بسیار شور حاوی انرژی اسمزی بالایی است. PRO با استفاده از غشایی نیمه تراوا، آب شیرین را از طریق انتقال غیرفعال آب از حلال جدا می کند. افزایش فشار اسمزی در سمت کشش با استفاده از ERD برداشت می شود. این انرژی می تواند برای جبران انرژی مورد نیاز برای پمپاژ فشار بالا استفاده شود. در حالی که چندین مطالعه نشان داده است که RO-PRO از لحاظ فنی مقرون به صرفه است، اما عملکرد و مزایای اقتصادی که هنوز تأیید نشده اند (Wan and Chung، 2018؛ Wang et al.، 2019). سیستم آبی Mega-ton در ژاپن یکی از تنها نیروگاه های مقیاس عملیاتی تا به امروز است که گزارش شده است که در یک آزمایش 12 ماهه احتمال کاهش 10٪ در SEC ، را داشته است.
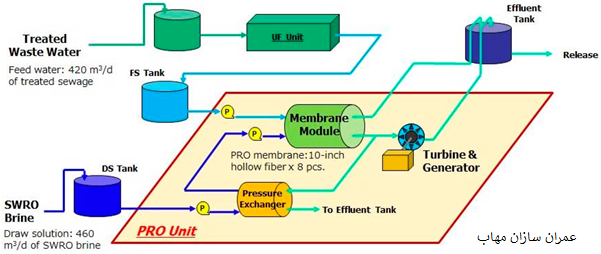
دستگاه های بازیابی انرژی در واحد های SWRO
چندین مطالعه نظری نشان داده است که RO-PRO می تواند به صرفه جویی در انرژی بیش از RO دست یابد (Wan and Chung، 2016، 2018؛ Li، 2017) به شرطی که نسبت بازیابی محدود باشد و واحد PRO دارای سطح غشای کافی باشد (Li، 2017؛ Wan and چونگ ، 2018). همچنین مشخص شد که پتانسیل بازیابی انرژی متناسب با شوری خوراک است (لی، 2017). علاوه بر صرفه جویی در هزینه بالقوه مرتبط با کاهش انرژی، بازیافت بخشی از کنسانتره RO از طریق PRO (“حلقه بسته” RO-PRO) می تواند هزینه سرمایه را به دلیل کاهش در مصرف آب دریا، واحدهای پیش تصفیه و تخلیه آب نمک به طور قابل توجهی کاهش دهد (وان و چونگ ، 2018). یکی دیگر از مزایای RO-PRO این است که کنسانتره RO تخلیه شده به سطح آب دریا رقیق می شود، و اثرات تخلیه را بر محیط زیست دریایی کاهش می دهد (Prante و همکاران ، 2014). چندین مانع برای زنده ماندن تجاری RO-PRO مشخص شده است. PRO مستعد ابتلا به رسوب زیاد است و نیاز به پیش تصفیه دارد (تلین و همکاران ، 2013 ؛ ژانگ و همکاران ، 2014).
پیکربندی های ترکیبی RO ، که به موجب آن SWRO با فن آوری اسمز عقب مانده فشار (PRO) یا اسمز رو به جلو (FO) ادغام شده است ، امکان کاهش قابل توجهی در انرژی کلی مورد نیاز را دارد: FO با کاهش انرژی پمپ مورد نیاز RO؛ PRO با برداشت و تبدیل انرژی اسمزی از کنسانتره RO به جبران پمپاژ RO. در حالی که تحقیقات نظری نشان می دهد تنظیمات ترکیبی RO می تواند به طور قابل توجهی SEC را کاهش دهد، اما مطالعات موردی در مقیاس عملیاتی برای حمایت از دوام تجاری هیبریدهای RO همچنان وجود دارد. موانع مشاهده شده شامل حساسیت PRO به رسوب دهی و جرم گیری، نواحی وسیع غشا مورد نیاز و در دسترس بودن یک جریان زباله رقیق مناسب است.
تحقیقات مداوم در مورد عملکرد غشا و پتانسیل ایجاد غشای مقاوم در برابر رسوب، دو روشی است که در آن هیبرید RO-PRO می تواند به یک واقعیت تجاری تبدیل شود. با تقاضای زیاد برای آب آشامیدنی در مناطقی که منابع آب شیرین مانند آب سطحی یا زیرزمینی ندارند، فن آوری های مختلف بالقوه برای رفع کمبود آب مورد بررسی قرار گرفته است. از زمان تاسیس ، فناوری SWRO جهش های بسیاری به سمت توسعه سیستم های کارآمد و پر بازده انرژی برداشته است. کاهش مصرف انرژی نیروگاه های نمک زدایی که مبتنی بر فناوری SWRO بودند، به عنوان محرک اصلی انقلاب فناوری در این زمینه ظاهر شد. بهبود عمر غشا و رد نمک، افزایش بازیابی و کاهش مصرف انرژی از معیارهای اصلی غربالگری از طریق فن آوری های موجود برای ترکیب در نیروگاه های نمک زدایی بوده است. از آن زمان، بسیاری از تحولات در این راستا رخ داده است. عمر غشا چند برابر شده است و مواد جامد در محصول اکنون به 100 میلی گرم در لیتر می رسند. علاوه بر این، بهبودهای 40-50٪ حاصل شده است. با بازیافت انرژی، بسیاری از نیروگاه های آب شیرین کن SWRO مصرف انرژی کل خود را به میزان قابل توجهی کاهش داده اند. اکنون با کمک دستگاه های بازیابی انرژی (ERD) می توان مصرف برق را کاهش داد و بهره وری نیروگاه آب شیرین کن اسمز معکوس آب دریا را افزایش داد.
تجزیه و تحلیل دستگاه های ایزوباریک در مقابل سانتریفیوژ نیز در این کار انجام شده است. مقایسه بین توربین بازیابی انرژی (ERT) تولید شده توسط Pump Engineering Inc. PEI و مبدل فشار (PX) تولید شده توسط سیستم های بازیابی انرژی (ERI) با استفاده از داده های جمع آوری شده از تجزیه و تحلیل آب ارائه شده و تولید کنندگان مربوطه انجام می شود. مشخصات دستگاه پیکربندی های مختلفی که برای این مقایسه به کار رفته است، برای کل تولید 240000 مترمربع در روز، به واحد آب شیرین کن SWRO جده اعمال شد. به عنوان یک نتیجه از این تجزیه و تحلیل ، مصرف انرژی خاص از تنظیمات ERT و PX به ترتیب 2.66 کیلووات ساعت در متر مکعب و 2.50 کیلووات ساعت در متر مکعب بود. با این حال تجزیه و تحلیل نشان می دهد که اگرچه پیکربندی PX بهترین مصرف انرژی خاص را به دست آورده است، به دلیل پایین بودن سرمایه و هزینه های نگهداری ، ERT از آن پسندیده است. بنابراین ، نتیجه نهایی این کار ، در این مورد خاص، مقرون به صرفه بودن پیکربندی ERT نسبت به پیکربندی PX است.
منابع
Abdelkareem, M. A., El Haj Assad, M., Sayed, E. T., and Soudan, B. (2018). Recent progress in the use of renewable energy sources to power water desalination plants. Desalination.
Altaee, A., Alanezi, A. A., and Hawari, A. H. (2018). Emerging Technologies for Sustainable Desalination Handbook – Chapter 2: Forward Osmosis Feasibility and Potential Future Application for Desalination.
Altaee, A., Zaragoza, G., Drioli, E., and Zhou, J. (2017). Evaluation the potential and energy efficiency of dual stage pressure retarded osmosis process. Appl. Energy.
Ang, W. L., Mohammad, A. W., Hilal, N., and Leo, C. P. (2015). A review on the applicability of intergrated/hybrid membrane processes in water treatment and desalination plants. Desalination.
Awad, A. M., Jalab, R., Minier-Matar, J., Adham, S., Nasser, S., and Judd, S. J. (2019). The status of forward osmosis technology implementation. Desalination.
Bhojwani, S., Topolski, K., Mukherjee, R., Sengupta, D., and El-Halwagi, M. M. (2019). Technology review and data analysis for cost assessment of water treatment systems. Sci. Total Environ.
Du, Y., Xie, L., Zhang, S., and Xu, Y. (2015). Optimization of reverse osmosis networks with split partial second pass design. Desalination.
Efraty, A. (2012). Closed circuit desalination series no-6: conventional RO compared with the conceptually different new closed circuit desalination technology. Desalin. Water Treat.
Ghaffour, N., Bundschuh, J., Mahmoudi, H., and Goosen, M. F. A. (2015). Renewable energy-driven desalination technologies: a comprehensive review on challenges and potential applications of integrated systems. Desalination.
Global Water Intelligence (GWI) (2016). IDA Desalination Yearbook 2016–2017, Water Desalination Report.
Gude, V. G. (2018). Sustainable Desalination Handbook—Plant Selection, Design and Implementation.
Guirguis, M. J. (2011). Energy Recovery Devices in Seawater Reverse Osmosis Desalination Plants with Emphasis on Efficiency and Economical Analysis of Isobaric versus Centrifugal Devices. Tampa, FL: University of South Florida.
Hailemariam, R. H., Woo, Y. C., Damtie, M. M., Kim, B. C., Park, K-D., and Choi, J-S. (2020). Reverse osmosis membrane fabrication and modification technologies and future trends: a review. Adv. Coll. Interface Sci.
Heihsel, M., Lenzen, M., Malik, A., and Geschke, A. (2019). The caron footprint of desalination–an input-output analysis of seawater reverse osmosis desalination in Australia for 2005–2015. Desalination.
Hermony, A., Sutzkover-Gutman, I., Talmi, Y., and Fine, O. (2014). Palmachim Seawater desalination plant—seven years of expansions with uninterrupted operation together with process improvements. Desalin. Water Treat.
Kadaj, E., and Bosleman, R. (2018). “Energy recovery devices in membrane desalination processes,” in Renewable Energy Powered Desalination Handbook: Application and Thermodynamics.
Karabelas, A. J., Koutsou, C. P., Kostoglou, M., and Sioutopoulos, D. C. (2018). Analysis of specific energy consumption in reverse osmosis desalination processes. Desalination.
Khan, M. A. M., Rehman, S., and Al-Sulaiman, F. A. (2018). A hybrid renewable energy system as a potential energy source for water desalination using reverse osmosis: a review. Renew. Sustain. Energy Rev.
Khan, S. U., Khan, S. U., Danish, S. N., Orfi, J., Rana, U. A., and Haider, S. (2018). “Nuclear energy powered Seawater Desalination,” in Renewable Energy Powered Desalination Handbook–Application and Thermodynamics.
Kim, J., and Hong, S. (2018). A novel single-pass reverse osmosis configuration for high-purity water production and low energy consumption in seawater desalination. Desalination.
Kim, J., Park, K., Yang, D. R., and Hong, S. (2019). A comprehensive review of energy consumption of seawater reverse osmosis desalination plants. Appl. Energy.
Kurihara, M., and Takeuchi, H. (2018). SWRO-PRO System in “Mega-ton Water System” for energy reduction and low environmental impact. Water.
Li, M. (2017). Reducing specific energy consumption of seawater desalination: staged RO or RO-PRO? Desalination.
Mekonnen, M. M., and Hoekstra, A. Y. (2016). Four billion people facing severe water scarcity. Sci. Adv.
Park, K., Kim, J., Yang, D. R., and Hong, S. (2020). Towards a low-energy seawater reverse osmosis desalination plant: a review and theoretical analysis for future directions. J. Membrane Sci.
Peñate, B., and García-Rodríguez, L. (2011). Energy optimisation of existing SWRO (seawater reverse osmosis) plants with ERT (energy recovery turbines): technical and thermoeconomic assessment. Energy.
Peñate, B., and García-Rodríguez, L. (2012). Current trends and future prospects in the design of seawater reverse osmosis desalination technology. Desalination.
Prante, J. L., Ruskowitz, J. A., Childress, A. E., and Achilli, A. (2014). RO-PRO desalination: an integrated low-energy approach to seawater desalination. Appl. Energy.
Ramato, A. T., Noviello, Y., Di Profio, G., Macedonio, F., Ali, A., Drioli, E., et al. (2019). Integrated membrane distillation-reverse electrodialysis system for energy efficient seawater desalination. Appl. Energy.
Sakai, H., Ueyama, T., Irie, M., Matsuyama, K., Tanioka, A., Saito, K., et al. (2016). Energy recovery by PRO in sea water desalination plant. Desalination.
Shemer, H., and Semiat, R. (2017). Sustainable RO desalination—energy demand and environmental impact. Desalination.
Urrea, S. A., Reyes, F. D., Suárez, B. P., and de la Fuente Bencomo, J. A. (2019). Technical review, evaluation and efficiency of energy recovery devices installed in the Canary Islands desalination plants. Desalination.
Valladares Linares, R., Li, Z., Sarp, S., Bucs, S. S., Amy, G., and Vrouwenvelder, J. S. (2014). Forward osmosis niches in seawater desalination and wastewater reuse. Water Res.
Voutchkov, N. (2018). Energy use for membrane seawater desalination—current status and trends. Desalination.
Wan, C. F., and Chung, T. S. (2016). Energy recovery by pressure retarded osmosis (PRO) in SWRO–PRO integrated processes. Appl. Energy .
Wan, C. F., and Chung, T. S. (2018). Techno-economic evaluation of various RO+PRO and RO+FO integrated processes. Appl. Energy.
Wang, Q., Zhou, Z., Li, J., Tang, Q., and Hu, Y. (2019). Investigation of the reduced specific energy consumption of the RO-PRO hybrid system based on temperature-enhanced pressure retarded osmosis. J. Membrane Sc